CeramTec Hermetics
For over 60 years, CeramTec has been a pioneer in the development of vacuum-tight ceramic-to-metal and glass-to-ceramic joints – products that prove themselves even in extreme scenarios. Whether it's extreme temperatures, high pressure, or chemically aggressive environments, our Ceramaseal® solutions offer hermetic assurance. We combine electrical insulation and leak-tightness to meet even the most demanding requirements in research and industry.
How would you like to realize your visions with components that perform reliably even under ultra-high vacuum or high-energy conditions? Discover with us how much performance is in every seal.

Are you interested in our products & solutions?
Go directly to our online shop.
Benefits of Advanced Ceramics Hermetic Solutions
- Excellent electrical properties: Outstanding insulation and high voltage resistance.
- Excellent mechanical strength: Robust against physical stress.
- Tight connection thanks to 100% helium leak test: High leak safety under extreme conditions.
- Low particle formation: Ideal for sensitive vacuum applications.
- High chemical resistance: Resistant to aggressive and corrosive substances.
- High purity: Use of high-purity materials for reliable performance.
- High temperature resistance: Reliable even under extreme temperatures.
- Excellent thermal conductivity: Efficient heat dissipation despite electrical insulation.
- Dimensional stability: Enables precision and reliability, even under extreme conditions.
- Reliability / high MTBF (Mean Time Between Failures): Durable and low-maintenance.
Pioneer for more than 60 years
Ceramaseal® ceramic-to-metal and glass-to-ceramic components and assemblies are ideally suited to support optical, gas, liquid, power, instrumentation, and sensing applications. CeramTec North America pioneered the science of Ceramaseal® ceramic-to-metal sealing more than 60 years ago and is still the world leader in ceramic-to-metal sealing technology today.
Hermetically Sealed to endure cold, heat or high pressure
Hermetic, vacuum-sealed Ceramaseal® products are built to endure extreme conditions. They stand up to ultra-high vacuum (UHV) environments, temperatures ranging from -269°C to 450°C, pressures in excess of 1,700 bar, corrosive or caustic environments, while maintaining an unsurpassed level of reliability and performance – Ceramaseal® products are known around the globe for their reliability. For ceramic-to-metal and glass-to-metal components, and glass-ceramic sealing technology CeramTec offers both standard and custom designs for use in vacuum, ultra-high vacuum, high-pressure, cryogenic, and high-temperature applications.
Vacuum-tight seals 100% helium leak tested
Ceramaseal® products from CeramTec undergo a 100% helium leak test on a dry leak detector to 1x10-9 atm cc/s He. Products can be tested to 1x10-10 atm cc/s on request. The vacuum-sealed ceramic-to-metal and glass-ceramic-to-metal components are designed for cryogenic applications and can withstand temperatures of up to 450°C with a leak rate of under 1x10-9 atm cc/s Helium; they are also suitable for use with currents of over 1,000 A and voltages exceeding 100 kV.
Our Combined Expertise
Research, design, manufacturing and testing for all Ceramaseal® components take place at CeramTec’s own facility in Laurens, South Carolina. CeramTec is the only North American supplier to offer the complete manufacture of advanced ceramics and sealing products under one roof. This ensures comprehensive technical control over the entire manufacturing process, from the start of production to the final product. New processes and materials are always undergoing testing at CeramTec in Laurens, where we also develop new processes and technologies to address the rapidly changing demands placed on ceramic-to-metal and glass-ceramic-to-metal seals along with the challenges involved in sensor technology and OEM market requests.
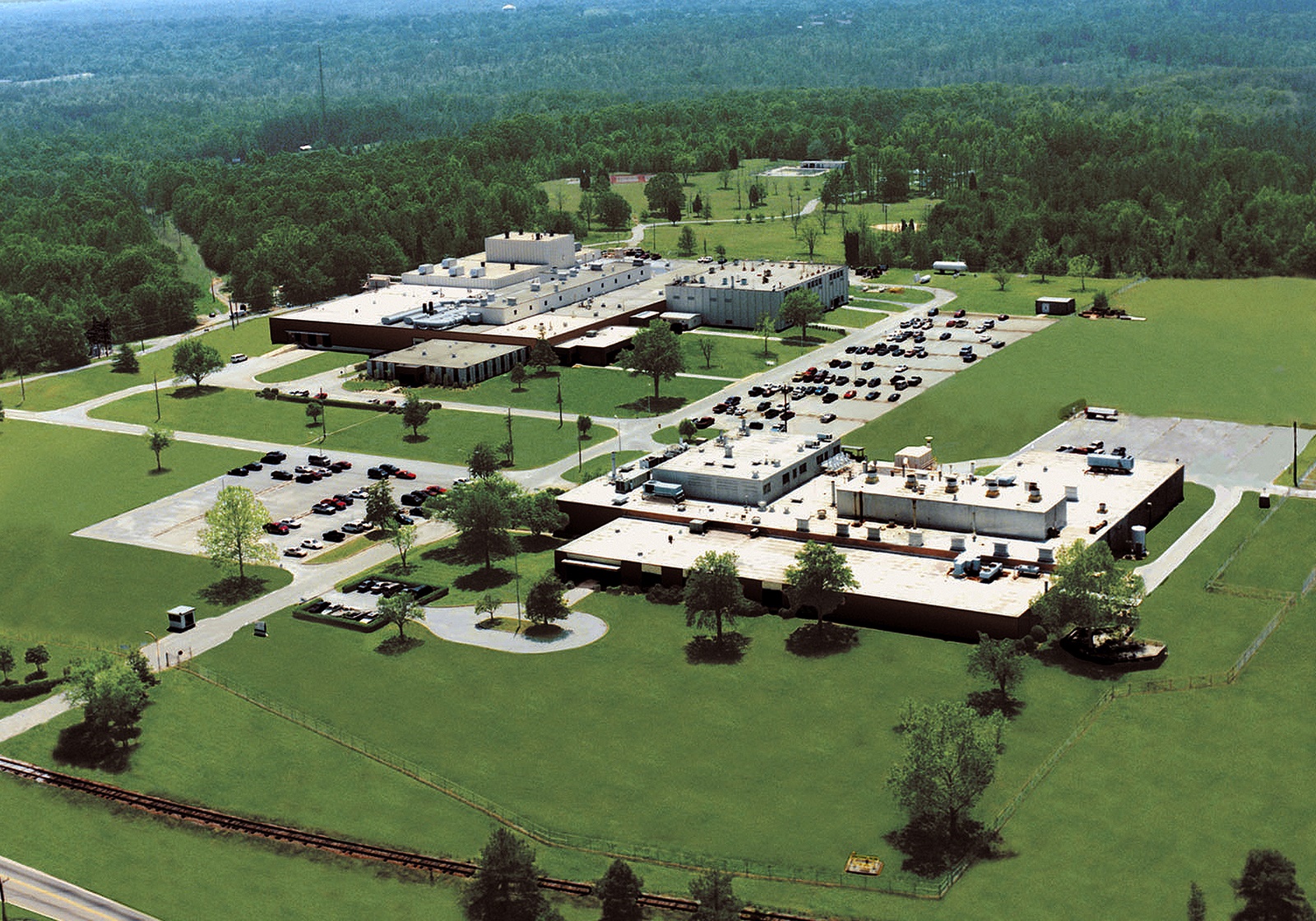