Advanced Ceramic Solutions in New Dimensions thanks to Additive Manufacturing
Additive Manufacturing with SiSiC and Al2O3
How can complex geometries, the highest material requirements and short production times be reconciled? CeramTec shows how 3D printing of high-performance ceramics is setting new standards in additive manufacturing. Materials such as silicon carbide (SiSiC) and aluminium oxide (Al₂O₃) are used to create components that are extremely resistant to temperature and wear and can be manufactured directly from CAD data in the shortest possible time and without the need for tools. Whether for prototypes or small series, discover the new design freedom and efficiency of ceramic additive manufacturing.
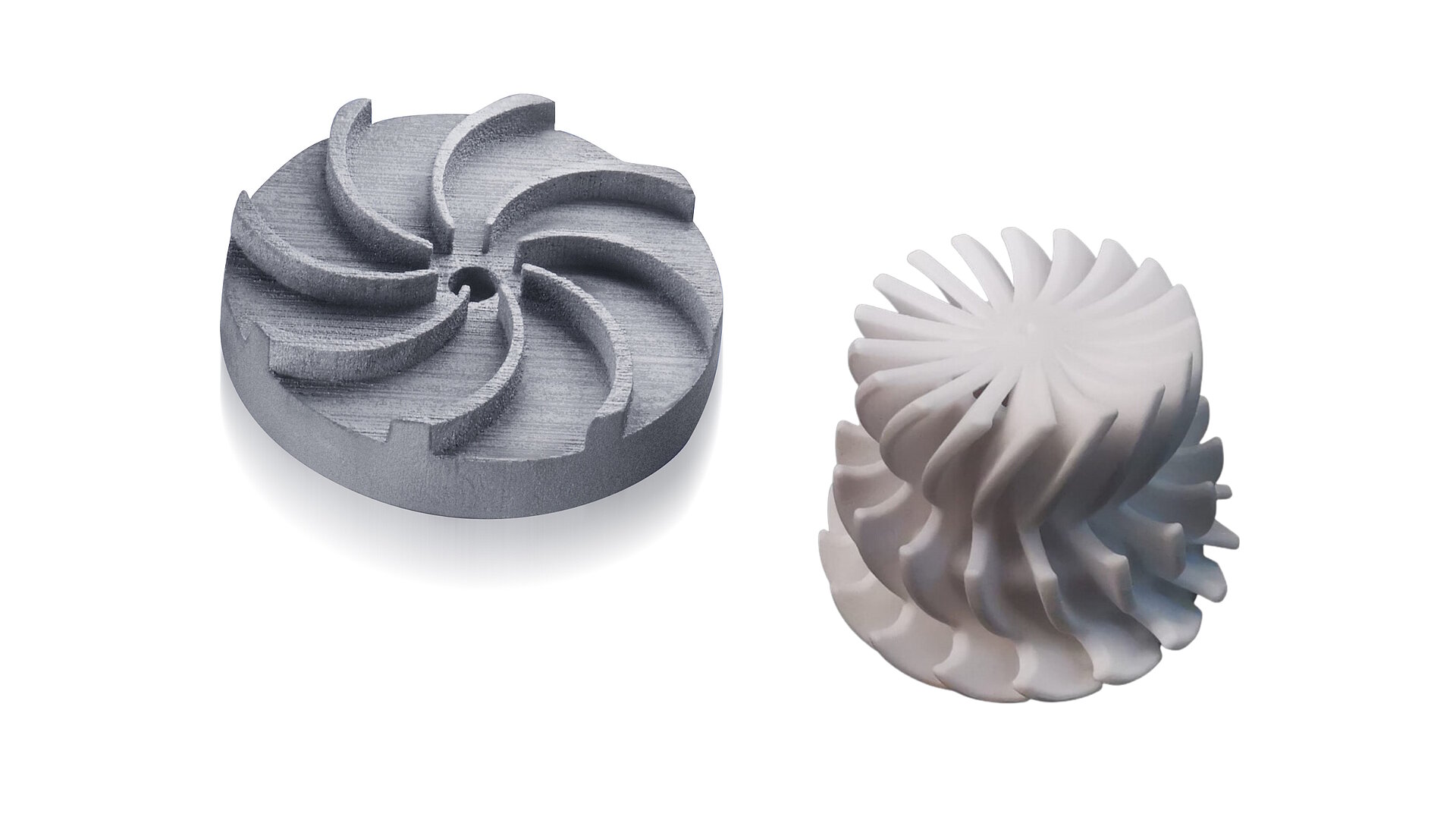
- Print directly from CAD data
- No tools required
- Cavities and undercuts possible
- Short production lead and tooling
- Maximum flexibility: design changes at the click of a mouse
- Digitisation of existing components possible
- Simultaneous production of several components on one 3D printer possible
Our competent service team supports you in product development - from the idea to the finished product.