Piezoceramics in Industrial Applications
CeramTec has decades of experience in the manufacturing of electroceramic components, sensors, transducers for the industrial equipment market. Are you looking for an alternative to lead-containing materials for your request? Then find out about our lead-free piezoceramic solutions based on BNT-BT.
We work in partnership with our customers to develop tailored solutions for specific industrial needs. Using our design expertise and specialist manufacturing capabilities, we can produce components within tight specifications in whatever quantity is required.
Precision-machined piezoceramic discs are used by many OEMs for automatic level and distance sensing in industrial equipment as well as for gas, liquid flow and level measurement systems.
Non-destructive testing equipment, many high-power ultrasonic applications such as ultrasonic cleaning, welding, inspection and sono-chemistry also use our piezoelectric ceramics as transducers.
Piezoceramic bimorphs are used as actuators in a wide range of industrial applications such as inkjet printer heads and viscosity meters. They are also used in coin and bank notes validation systems.
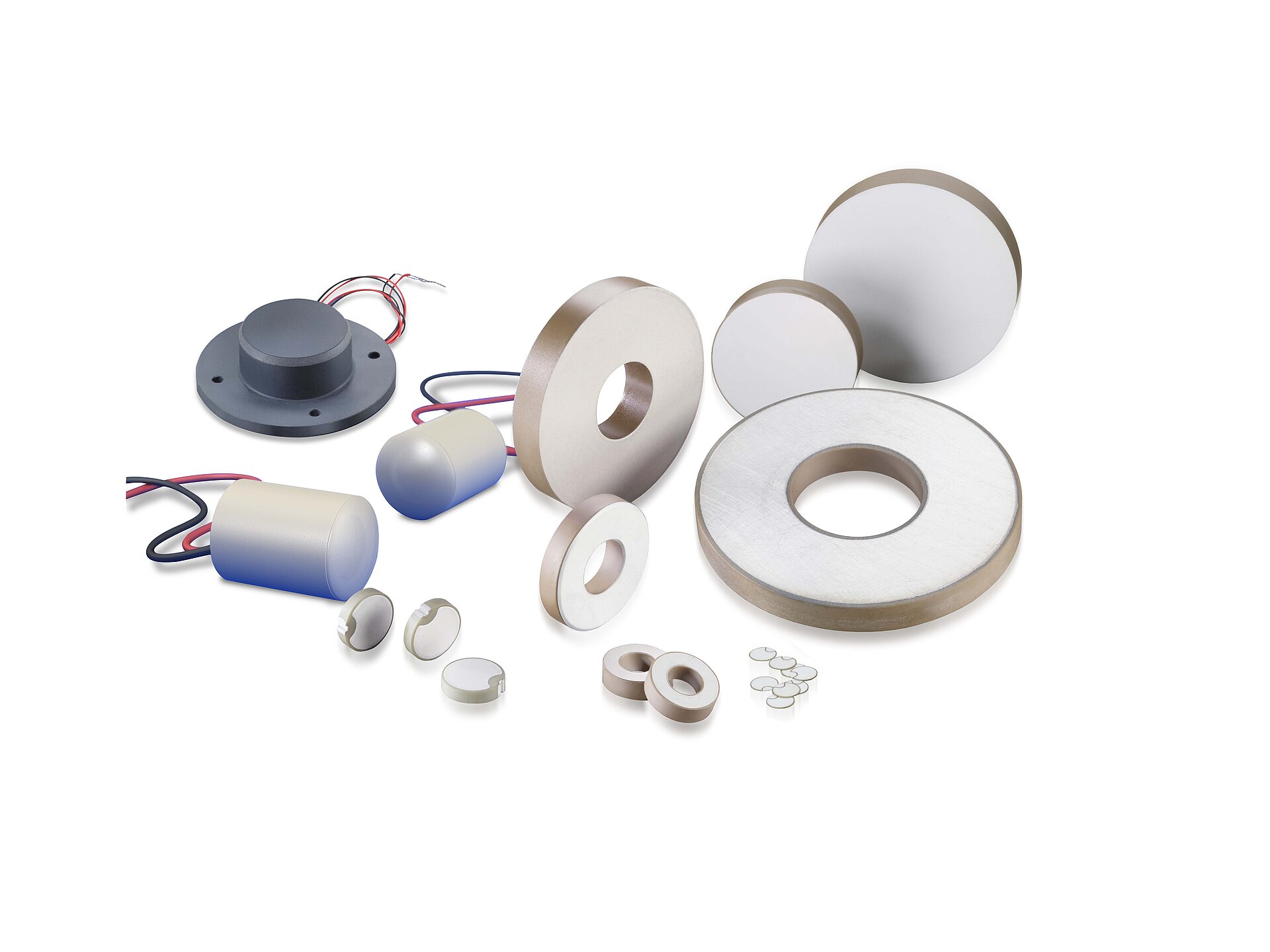
Ultrasonic level measurement takes place using propagation time measurement of an airborne ultrasonic signal that is transmitted and then reflected by the substance being measured. One key advantage of this system is that it operates on a “non-contact” basis, meaning that is also possible to measure the level of solids in silos, for example. A disadvantage is that the accuracy of the measurement depends on the reflection properties of the respective substance. For the piezoceramic transducer to measure accurately, a certain amount of the wave it emits must be reflected. If the wave front is scattered too much or absorbed by the stored materials, no useful measurement is possible.
Designs: Discs, rings other special designs
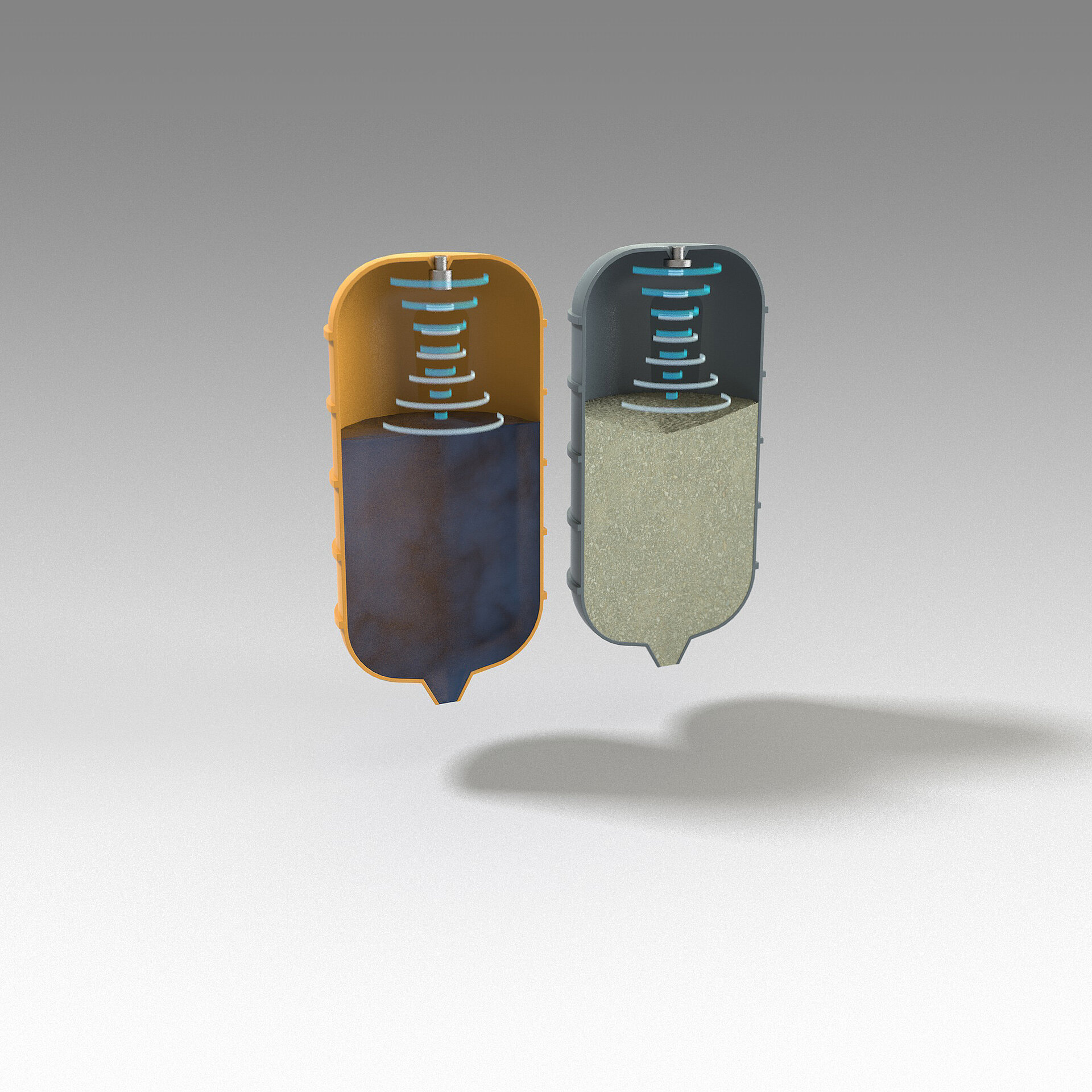
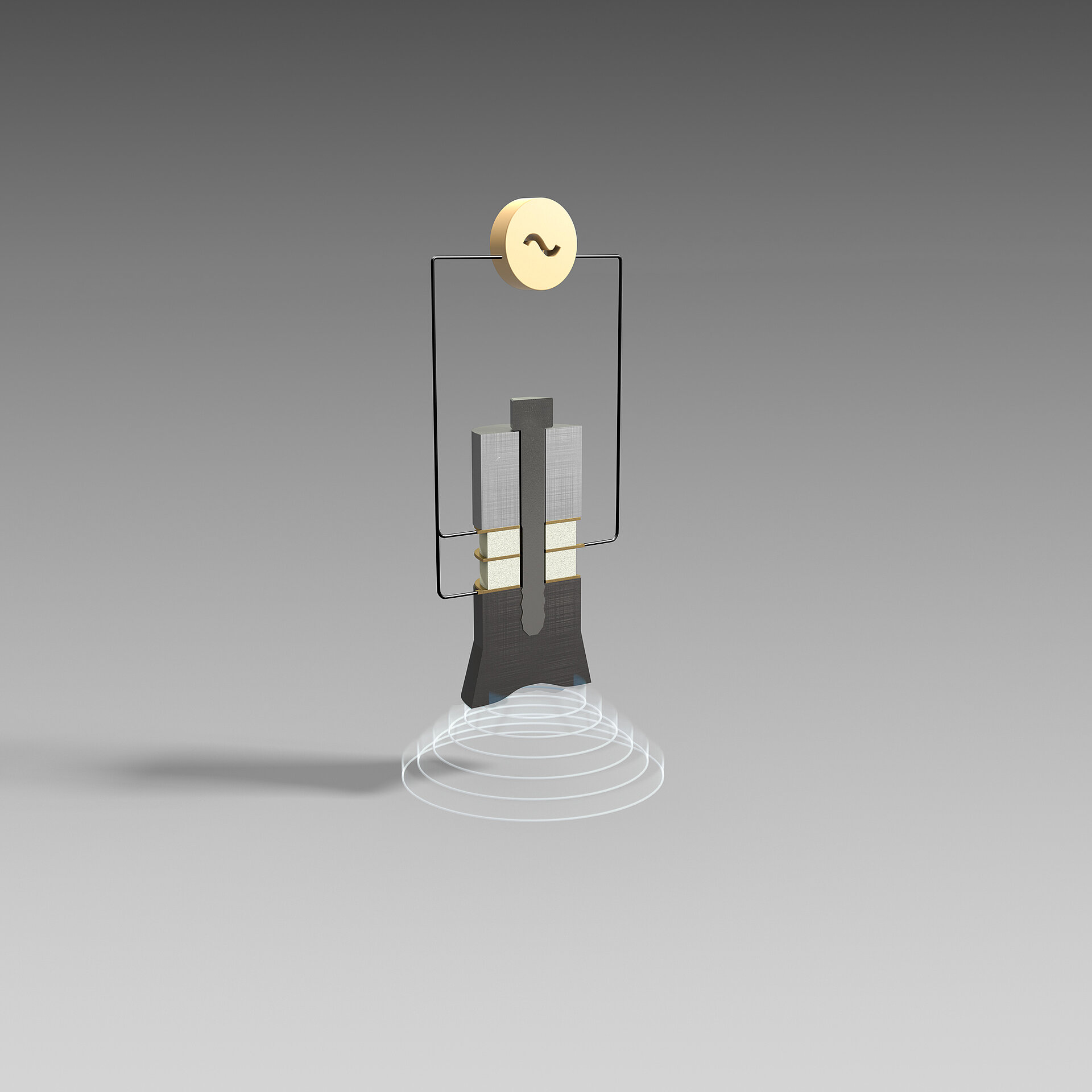
Ultrasonic cleaning is a topic that covers a wide range of designs from small eyeglass cleaning baths for opticians all the way to 20m-long industrial cleaning plants with automatic conveyor systems. Ultrasonic cleaning works by creating cavitation in a cleaning liquid by means of high-power ultrasonic waves. Cavitation is the formation (due to pressure differences in the fluid) of tiny local gas bubbles, which implode after a very short period of time. The cavitation intensively cleans the contaminated surface of the substance, even with complicated shapes. The ultrasonic energy is transmitted into the fluid via the bottom and the walls of the cleaning tank, or via immersed transducers. The piezo composite transducers that generate the ultrasonic waves usually consist of at least two piezoceramic rings mechanically preloaded with metallic end pieces. In very small cleaning baths, a single piezoceramic round plate is glued to the bottom of the tank.
Designs: Discs or rings
Ultrasonic welding takes advantage of the friction energy generated by the ultrasound at the boundary surfaces. When two preforms are pressed together at their connecting surfaces and excited using high-frequency ultrasound, the surfaces of the two parts generate so much energy that their connecting surfaces fuse together. This works with both metal and plastic parts. The ultrasonic energy is fed to the parts to be joined via a sonotrode, which amplifies the ultrasound generated by the piezo transducer. The piezo transducer consists of two or more piezoceramic rings that are mechanically pre-stressed using two metallic end pieces. Ultrasonic welding has established itself in industry as a very fast, cost-effective and reliable joining technology.
Design: Rings
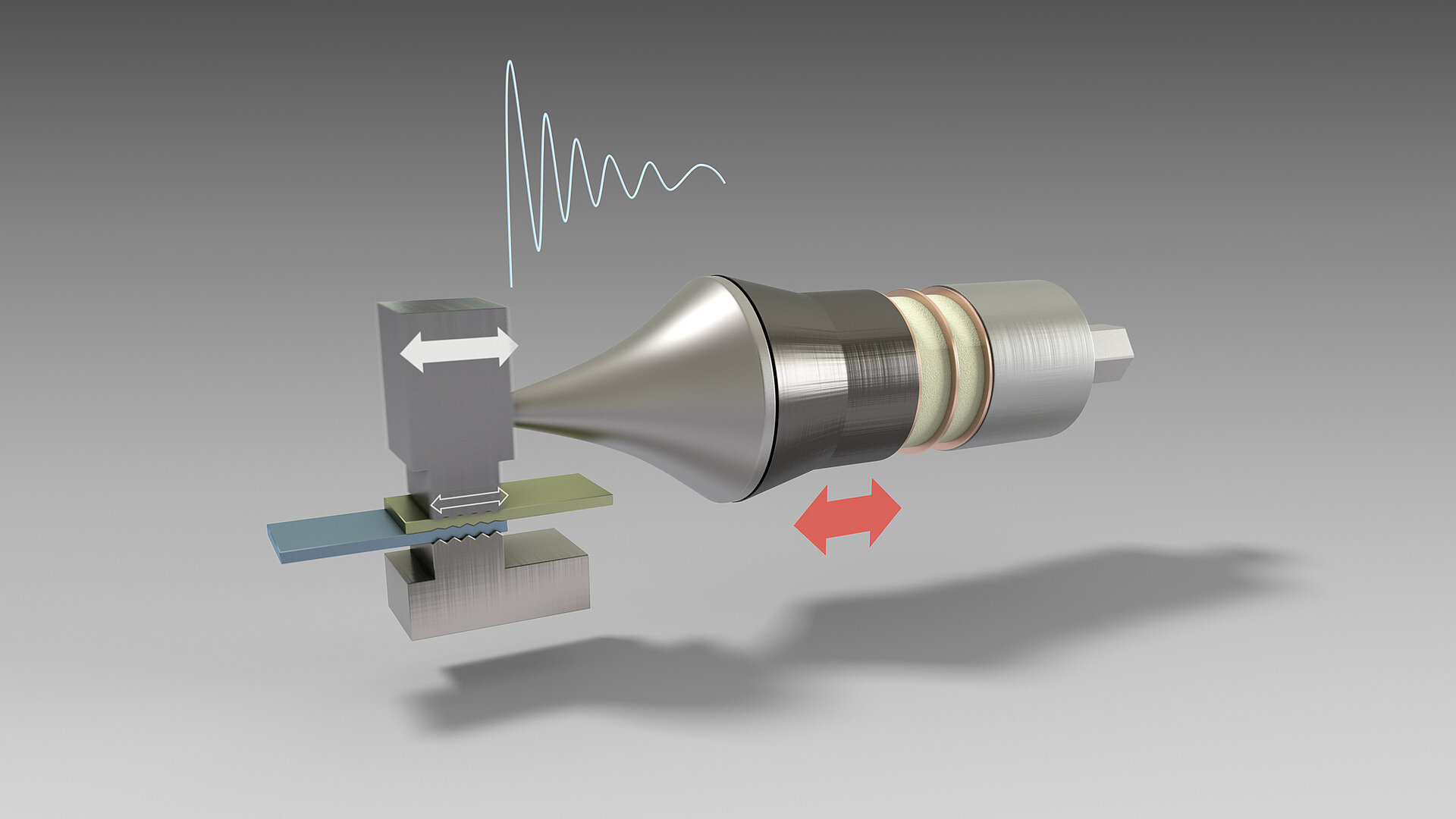
The design layout and the generation of ultrasonic waves is identical to ultrasonic welding, except that a tool for machining the material is coupled to the end of the sonotrode and an additional suspension is used which acts like an abrasive. The tool is excited to produce ultrasonic vibrations in the feed direction, which also make the abrasive particles in the water suspension vibrate. For a fraction of a vibration cycle the particles are frictionally engaged with the workpiece and tool. The workpiece is microscopically cut during these impacts. This process makes it possible to machine almost any material, from glass to hard metal. The advantage of this machining method is its great precision and the high-quality surface finish of the machined part.
Design: Rings
In mechanical, plant and tool engineering, the standard for many years has been to produce maximum load resistance with a minimum of material. The precondition for this is that the materials or semi-finished products used are free of defects or inhomogeneities. Non-destructive material testing allows for comprehensive quality assurance in the production process. Of all the testing methods used in industry, the reflection technique is the most widespread. In this method, a piezoceramic transmitter is connected either directly or via a liquid or solid coupling medium to the workpiece to be tested. The piezoceramic transducer radiates an ultrasonic wave package into the test piece where it is either reflected if there are defects or inhomogeneities, or passes through the test piece without hindrance. Reflected sound waves are received again by the same piezo transducer and detect defects in the material.
Designs: Round discs, rectangular plates, square plates
Piezoceramic components in sonar systems are used for recognition, ranging and navigation in a wide range of underwater applications such as echo sounders for small boats to measure water depth or sonar arrays for large ships to locate schools of fish, to monitor trawl nets or for seabed mapping.
Designs: Round discs, rectangular plates, square plates
A piezoceramic disc sends a short ultrasonic air wave in the direction of the object whose distance is to be measured. The sound wave is reflected by this object and received again by the same piezoceramic part. The piezoceramic part operates here as sender and receiver (time multiplex mode). The piezoceramic part normally has an adaption layer on the radiating side to match the acoustic impedance of the transducer to that of the air. The frequency used by the transducer (resonance mode) here depends on the desired range and the resolution. The higher the frequency, the higher the resolution and the shorter the range, and vice versa. If the wavelength resulting from the frequency is large in comparison to the size of the transducer, the result is a spherical-shaped radiation of the wave front. If the wavelength is shorter than the transducer, it is radiated straight (in a close angle). Directed radiation is desired in almost all cases. The distances that can reasonably be measured using these systems are between 0.25 m and 10 m. This application can be used for a variety of purposes in industrial automation, for example, for distance measurement, as a limit monitor or as a counter (an object is registered every time it passes through the measuring range).
Design: Round discs
In ultrasonic flow rate measurement a distinction is made between two different measuring principles: the Doppler effect and the analysis of the traveling wave time. In both cases a piezoceramic transducer positioned on the tube wall generates ultrasonic waves, which are then transmitted into the liquid diagonally to the direction of flow. The Doppler evaluates the frequency shift of the ultrasonic waves, which are reflected by stray particles in the liquid. The greater the flow speed of the liquid, the greater the frequency shift between the radiated and the reflected wave front. Only one piezo transducer sending and receiving at different times is needed for this measuring method. The traveling wave time principle always employs two piezoceramic transducers positioned offset to the direction of flow. They send or receive alternately pulse-shaped ultrasonic wave packages against the direction of flow and in the direction of flow. In each case there is a superimposition of sound propagation speed and flow speed. The flow speed is then proportional to the reciprocal value of the propagation time difference in and opposite to the direction of flow. The advantage of this measuring method is that the measurement is independent of the sound propagation speed and therefore also the medium. This enables the measurement of both liquids and gases.
Design: Round discs or plates
Pipeline leak detection is used to determine if and in some cases where a leak has occurred in systems which contain liquids and gases. If the pipeline is a plastic pipeline and the medium is water (household water supplies), then a hydrophone can be used for leakage detection. The hydrophone consists of a piezoceramic tube and plastic housing and analyses the noise generation in the system to detect the leak. The sensor works as an "underwater microphone".
Design: Round discs or tubes
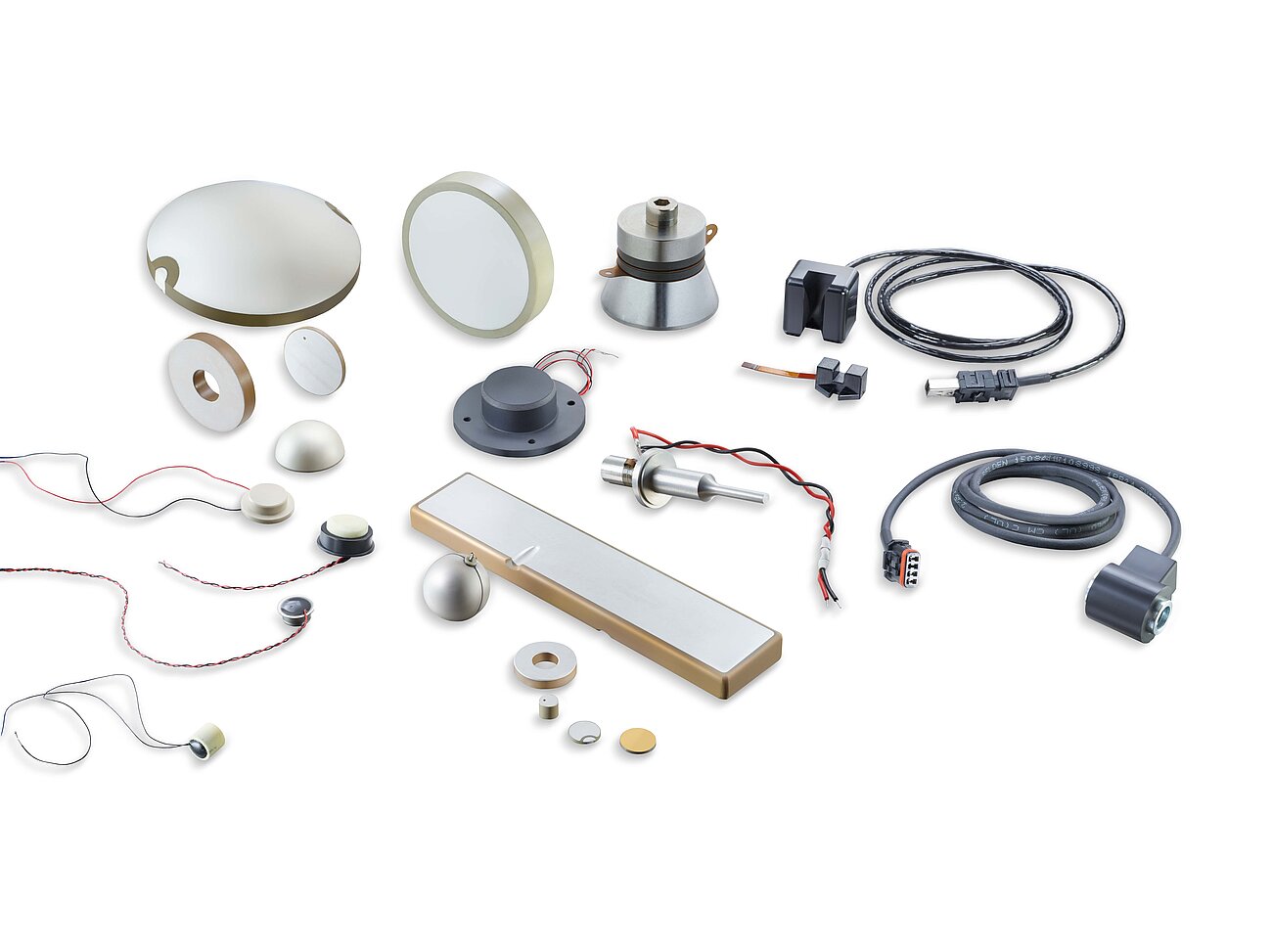