CeramCool® Principle & Function
Chip-on-heat-sink on the metalized surface of CeramCool® heat-sinks makes it possible to achieve an extremely compact design for the entire cooling system. Using ceramic as the material for the heat-sink ensures outstanding thermal conductivity and electrical insulation; the closer it is used to a source of heat, the greater the cooling advantage it offers.
Heat-sensitive semi-conductor components are often mounted onto standard substrates. They need to offer suitable thermal conductivity in addition to electrical insulation. The result is often a “sandwich component” with multiple layers made of different materials. Each layer introduces its own set of risks, thereby restricting thermal conductivity. With CeramCool®, however, these layers are not needed, as the substrate itself is already the heat sink, because high-performance ceramics in the form of aluminium oxide or aluminium nitride are used here.
Electrical insulation and thermal conductivity
Ceramics combine two essential properties: electrical insulation and thermal conductivity. They offer good electromagnetic compatibility and have a thermal expansion coefficient close to that of semiconductor materials. Unlike other materials, ceramics feature the same thermal expansion coefficient and thermal conductivity in all directions. Moreover, ceramics are watertight and UV and corrosion-resistant.
The simplified design combined with the direct, permanent bonding between heat-sensitive electronic components and the CeramCool® surface – chip-on-heat-sink – create the ideal operating conditions.
CeramCool® Chip-on-Heat-Sink
CeramTec developed chip-on-heat-sink as a revolutionary process for mounting a heat source such as an LED or power semi-conductor directly onto a metalized heat-sink via soldering or Ag sintering. This achieves an optimum thermal connection with the coolant (air or liquid).
CeramTec's chip-on-heatsink ultimately describes a design concept for significantly reducing thermal resistance, the number of components and installation space. CeramCool® is a heat sink and insulator in one.
- No additional metal heat sink: You can metallise the track layout directly onto the heat sink.
- No additional isolator: You can sinter or braze your semiconductor directly.
- Direct thermal contact: Interfaces disappear and thermal resistance is reduced.
CeramTec has two materials at its disposal for manufacturing CeramCool® heat-sinks that have had a proven track record in the electronics industry for many years: Rubalit® aluminum oxide (Al2O3) and Alunit® aluminum nitride (AlN).
CeramCool® Liquid Cooling Performance Comparison
To prove the performance capability of the CeramCool® principle in liquid-cooled systems, a directly metalized heat-sink (chip-on-heat-sink) went head to head with a conventional liquid cooler with a soldered-on DCB. During an exhibition, identical load current was applied to both cooling solutions’ IGBTs until a constant temperature was reached. Then the cool down curve was measured. The result: With the same power supplied, ΔT – and thus the thermal resistance – in the CeramCool® system design was only half that of a conventionally designed system.
Comparison: Chip-on-Heatsink/Conventional structure of a Powermodule (Pin = 100 W)
This makes CeramCool® Liquid Cooling one of the most efficient and reliable liquid cooling systems on the market. No other design can achieve this and still assure such a long lifetime. The ceramic heat-sink is perfectly electrically insulated and inert. It can be populated with electrical circuits and advanced components without creating any thermal barriers. This ceramic system’s efficiency grows with the power density.
Cooperation for optimal cooling performance
CeramTec and the Fraunhofer Institute for Integrated Systems and Device Technology (IISB) in Erlangen are working together to develop innovative cooling solutions for power electronics for a drive inverter.
This joint project focuses on thermal management using ceramic coolers with applied metallisation. This makes it possible to apply semiconductor chips directly to the ceramic cooler (chip-on-heatsink). The collaboration focuses on the development of a module design that uses ceramic coolers to efficiently dissipate heat from the SiC chips, makes the best possible use of the chip area and keeps the size of the cooler as small as possible. In this way, high electrical power, which entails high heat generation, can be reliably cooled in a small space and the sizes of power modules can be miniaturised. In the measurements carried out by IISB, it was possible to halve the thermal resistance compared to state-of-the-art modules.
- Would you like to learn more? Discover our free info paper as well as the presentation with all measurement results.
- Information to go - Discover our brochure Thermal Management with Ceramic Coolers
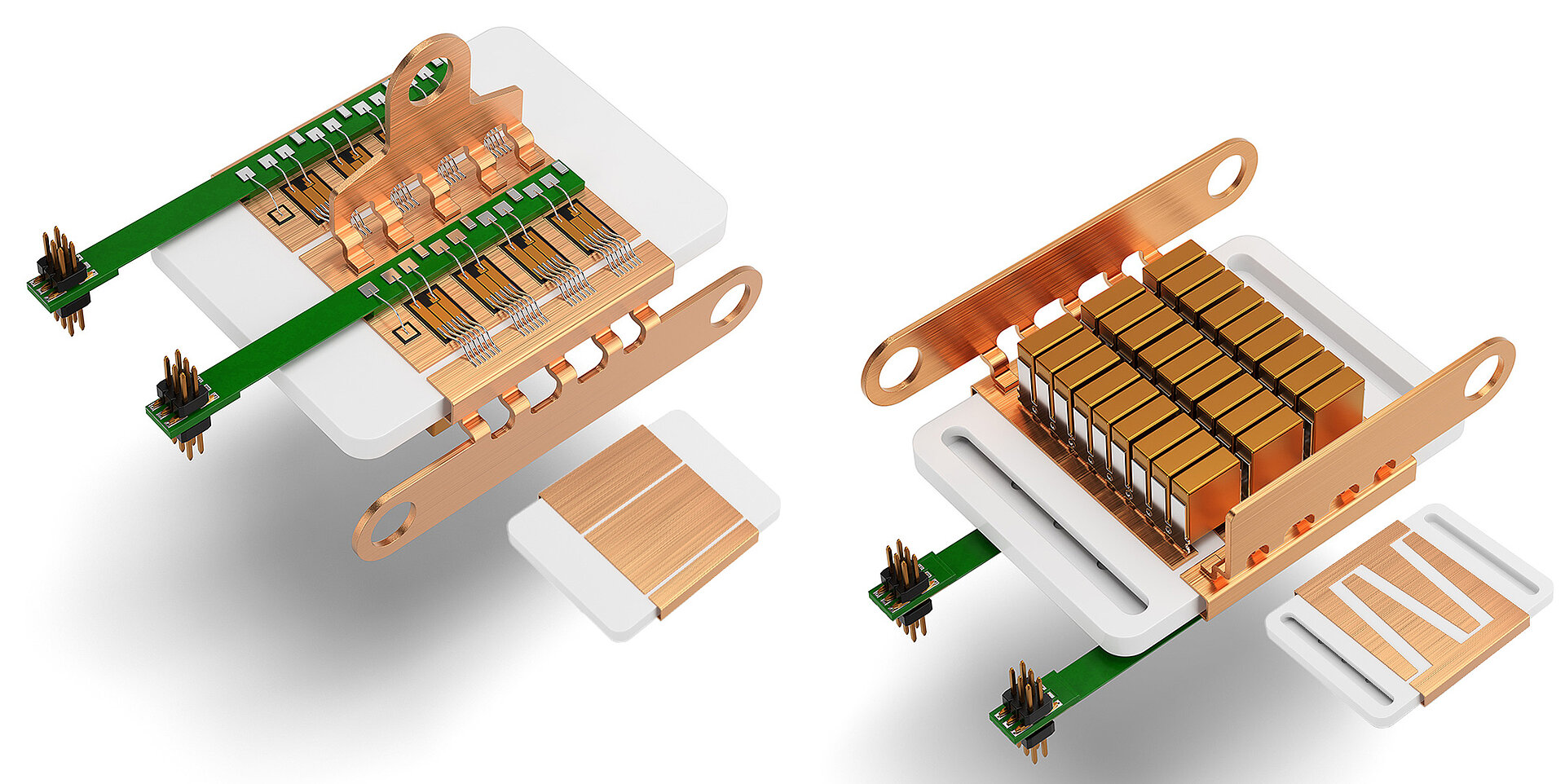
CeramCool® Air Cooling Performance Comparison
A fin heat-sink was optimized for 4W cooling and used as a basis for comparison in order to prove the performance capability of the CeramCool® principle in air-cooled systems. The result: The total thermal resistance of the ceramic Rubalit® design is at least 13% better than that of an aluminum assembly with an identical design. Using Alunit® even helped CeramCool® achieve a minimum improvement of 31%.
Air-cooled CeramCool® fin heat-sinks have a proven track record in applications with less extreme power densities - such as LED modules.