Integrated SiC-Power-Module on Ceramic Heat Sink
In cooperation with the Fraunhofer Institute for Integrated Systems and Device Technology (IISB) in Erlangen, we have developed innovative cooling solutions for the power electronics of a drive inverter.
Our SiC power module with advanced AlN ceramic cooler is mainly used when low thermal impedance, high inductance and high power density (combined with low weight) are required.
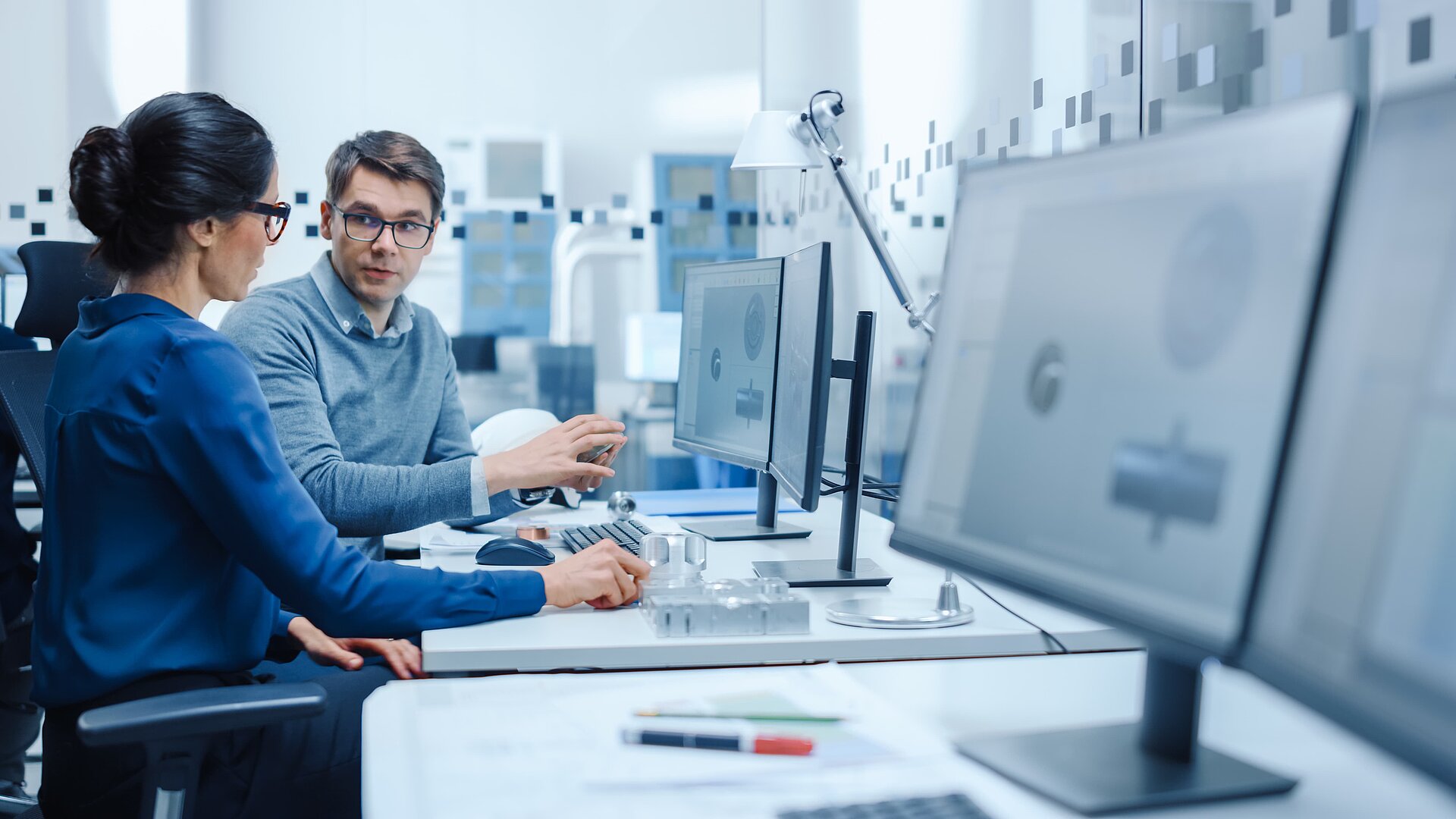
CeramTec and the Fraunhofer Institute for Integrated Systems and Device Technology (IISB) in Erlangen are working together since 2021 to develop innovative cooling solutions for power electronics for a drive inverter.
This joint project focuses on thermal management using ceramic coolers with applied metallisation. This makes it possible to apply semiconductor chips directly to the ceramic cooler (chip-on-heatsink). The collaboration focuses on the development of a module design that uses ceramic coolers to efficiently dissipate heat from the SiC chips, makes the best possible use of the chip area and keeps the size of the cooler as small as possible.
In this way, high electrical power, which generates a lot of heat, can be reliably dissipated in a small space and the sizes of power modules can be miniaturised. In the measurements carried out by IISB, it was possible to halve the thermal resistance compared to state-of-the-art modules.
CeramCool® Chip-on-Heat-Sink
CeramTec has developed the chip-on-heat sink as a revolutionary process for soldering or Ag-sintering a power semiconductor directly onto a metallised ceramic heat sink. This achieves an optimum thermal connection with the coolant (air or liquid).
CeramTec's chip-on-heatsink ultimately describes a design concept for significantly reducing thermal resistance, the number of components and installation space. CeramCool® is a heat sink and insulator in one.
- No additional metal heat sink: You can metallise the track layout directly onto the ceramic heat sink.
- No additional isolator: You can sinter or braze your semiconductor directly.
- Direct thermal contact: Interfaces disappear and thermal resistance is reduced.
- Significant Rth savings by use of ceramic cooler compared to state of the art power modules possible
- Further improvement of Rth by optimized structure → trade off regarding thermal performance and pressure drop
- Reduction of overall system volume & weight by thickness of ceramic cooler and additional degrees of freedom
Power-Module Design
- 1200V full SiC - half bridge with sintered semiconductor devices on CeramTec AlN-ceramic-cooler
- Low Rth‘ = 0.15 K*cm²/W for high current capability
- Low module inductance by
- module integrated ceramic capacitor on back side of ceramic cooler
- Cooler edge encompassing metallization
- Uncritical interfaces for easy system application
- Module design scalable depending on current requirements
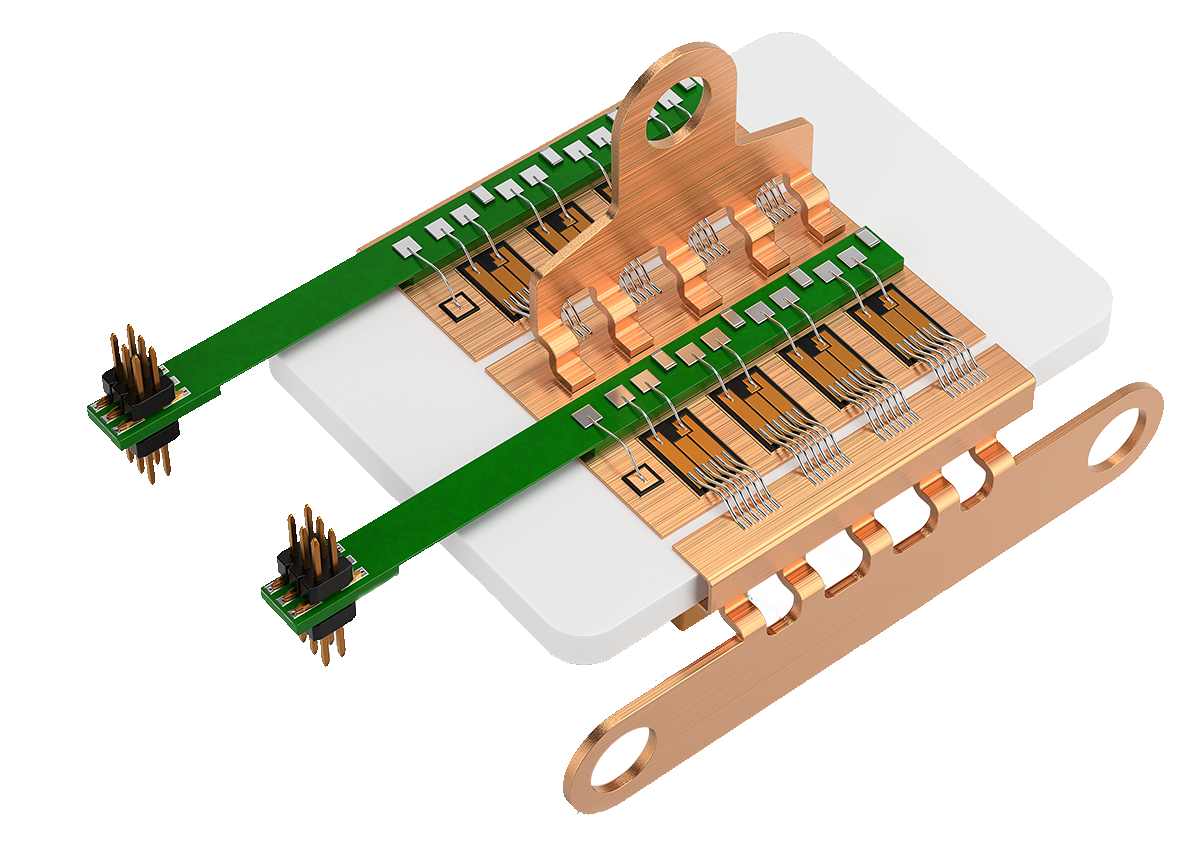
SiC-Power-Module on Ceramic Heat Sink
- 1200V full SiC - half bridge with sintered semiconductor devices on CeramTec AlN ceramic cooler
- Excellent thermal properties (confirmed by measurements)
- Low module inductance (confirmed by measurements)
- Module integrated ceramic capacitor on back side of ceramic cooler
- Cooler edge encompassing metallization